29th International ALTA Conference
Critical Battery Minerals
電池的關鍵礦物
Advances in Mining & Metallurgical Processing Methods for Extraction, Recovery & Recycling of Critical Minerals
2025年5月21日 – 22日 ALL TIMES AWST
Wednesday, 21 May
07:00Presenter Briefing
07:30Registration Open
07:30Arrival Tea and Coffee in the Exhibit Hall with Poster Viewing
CRITICAL BATTERY MINERALS MARKET & PRODUCTION
Taking the “Critical” out of Critical Battery Materials
Adrian Griffin, Principal, Future Technology Trust
In the two years from the 2022 peak, lithium prices have slumped 85%. Over the same period both nickel and cobalt prices have halved and many of the other ‘critical’ battery materials have also saw price volatility. Perceived shortages shifted to over-supply while battery chemistry evolved to become more sustainable and provide better value for consumers. Processing advances have improved the recovery of lithium and opened the floodgate for deposits once not considered to be economic. A global push for sustainability and environmental best practice is driving recycling and changing supply chain dynamics. This will improve access to material inputs, provide greater raw material availability and improve supply chain security thus reducing the criticality of battery materials.
Lithium for Next-Generation Batteries: From Mines to Metals
Andrew Nissan, PhD, Senior Director, Battery Strategic Sourcing, Lyten
Most lithium indexes and reports focus entirely on lithium carbonate and lithium hydroxide production; however, to power the next generation of cells, lithium metal is required as the anode material. To optimise lithium metal for pricing and performance a different process flow is required from the mines to metal.
McNulty Ramp-Up Curves of Critical Mineral Projects
Niels Verbaan, Director, Technical Services (Hydrometallurgy), Metallurgy & Consulting, SGS, Canada
Many of the McNulty curves presented to date have been based on traditional commodities. Industry electrification, climate change technologies, as well as the current trend to develop domestic supply chains for non-traditional or critical commodities (such as rare earths, graphite, lithium, nickel, cobalt, gallium, germanium, and antimony) have led to new critical mineral projects being developed. While traditional commodity projects can bench mark against existing projects to assist in derisking and generating capital and operating cost estimates, this is more difficult for critical mineral projects. Without bench marking, additional engineering studies supported by pilot and/or demonstration plant operations may be required. This paper will present McNulty Ramp-up Curves of recent critical mineral projects using production data out of the public domain, and where possible provide comment on the extent of additional engineering and pilot studies carried out to derisk these projects.
Lithium Future: Opportunities & Challenges
Anand Sheth, Founding Chairman, International Lithium Association
An industry that experiences exponential growth and attention, from a very small (and low profile) base, faces many challenges in building its supply chain. The Lithium Battery value chain is a new and evolving sector, mainly in the last decade, and rapid technological innovations brings its challenges at every step of the supply chain, from resources to processing to refining to recycling to end markets, etc. This presentation discusses the various challenges and the opportunities this presents if the market is going to reach its full potential.
10:35Morning Tea in the Exhibit Hall with Poster Viewing (Sponsorship Opportunity Available)
RARE EARTH AND OTHER CRITICAL MINERAL PROCESSING
Sustainable Rare Earth Recovery: Insights from the Meteoric Caldeira Rare Earth Project Pilot Studies
Gavin Beer, General Manager, Met-Chem Consulting
Meteoric Resources has developed and piloted a flowsheet for recovering rare earths from the Caldeira ionic clay-hosted deposit in Minas Gerais, Brazil. This integrated process minimises CAPEX and OPEX while prioritising the highest standards of environmental stewardship.
Continuing Developments at the Boland ISR Rare Earth Project: The Vision for Low Cost, Low Impact, Domestic Rare Earth Production
Robert Blythman, Exploration Manager, Cobra Resources plc
Cobra Resources are progressing the ISR amenability story of the Boland Rare Earth Project on the Eyre Peninsula of South Australia. Rare earth recoveries, acid consumption, and permeabilities have been assessed in bench scale tests at ANSTO, and continue to demonstrate ISR amenability in the Narlaby Paeleochannel for rare earths.
Process Design Addressing Challenges in Recovery of Rare Earths from the Songwe Hill Deposit
Elizabeth Ho, Sr Hydrometallurgist, Minerals Grp, ANSTO Australian Nuclear Science & Technology Org
This presentation will outline process options evaluated for Mkango Resources' Songwe Hill rare earth deposit which contains the rare earth fluorocarbonate minerals, synchysite (Ca(Ce,La,Nd)(CO3)2F) and parisite (Ca(Ce,La,Nd)2(CO3)3F2), as well as fluorapatite Ca5(PO4)3F. The process development for the flotation concentrate was targeted at the particular mineralogy of the deposit and a relatively simple flowsheet was developed that elegantly addressed challenges relating to the simultaneous presence of phosphate, fluoride and calcium.
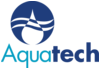
Greg Mandigo, Director Evaporation & Crystallization Technology, Evaporation & Crystallization Technology, Aquatech
Lithium salts are produced from sources ranging from spodumene , brines, clays and a variety of other unconventional sources. Where the final lithium product is a high-purity lithium carbonate (suitable for battery manufacturing), the carbonation process is an essential step. While the carbonation of lithium is often viewed simplistically as a precipitation reaction, there is an opportunity to shift this paradigm to unlock the hidden potential behind deliberate (controlled) crystallization of lithium carbonate. Lithium carbonate crystallization performed with established growth-type crystallizer technology delivers a simple and robust process for not only the carbonation step itself but also provides synergistic implications for the rest of the production process.
12:20Sponsored Presentation (Opportunity Available)
12:35Networking Luncheon (Sponsorship Opportunity Available)
RARE EARTH AND OTHER CRITICAL MINERAL PROCESSING
Mineral Characterisation of QEM's Julia Creek Oil and Vanadium Deposits
Elizaveta Forbes, PhD, Associate Professor, University of Queensland
QEM Ltd is undertaking a pre-feasibility study for the development of the Julia Creek vanadium and oil shale project in Queensland. The deposit contains kerogen which can be extracted as a hydrocarbon resource, and vanadium which is hosted in the clay and oxide phases, primarily in montmorillonite. This work constitutes the mineral characterisation with a view to determining the most viable processing routes for oil and vanadium recovery.
Processing Dysprosium From Local Rare Earth Metal Hydroxide Concentrate as Dopant Material for Dosimeter Applications
Nofriady Aziz, Director Nuclear Facility Management, BRIN NationalResearch & Innovation Agency
Dysprosium (Dy), a rare earth metal from tin mining by-products, is valuable for use in advanced materials but challenging to separate from other similar REE elements. Research focuses on deposition and extraction processes from REE hydroxide concentrate to obtain high-purity Dy, crucial for radiation detector applications. Key findings include optimal precipitation pH levels for major REEs and the efficiency of a 5% TBP extractor, highlighting the potential of nuclear technology to enhance industrial and environmental safety.
LITHIUM PROCESSING
From Alpha to Beta: Deciphering the Reaction Kinetics and Mechanisms of Spodumene Calcination-Review of Recent Evidence
Bogdan Dlugogorski, PhD, Distinguished Research Professor, Science & Technology & Energy & Resources, Charles Darwin University
Recent studies reveal the intricate mechanisms in transforming a-spodumene to ß-spodumene during calcination, a critical step for lithium extraction. The reaction involves complex reconstructive transformations with high activation energies. Existing kinetic models show significant discrepancies and limitations. This presentation reviews recent evidence to decipher these reaction kinetics and mechanisms focusing on: challenges in achieving complete a-to-ß transformation in industrial settings, optimising calcination temperature and duration for efficient lithium recovery, impact of particle size on reaction kinetics, and process efficiency, Comparative analysis of kinetic models and their industrial relevance, sustainable alternatives to traditional high-energy calcination methods.
15:05Afternoon Tea in the Exhibit Hall with Poster Viewing (Sponsorship Opportunity Available)
A Review of the Application and Potential for Ore Sorting to Upgrade Lithium Ores
Tony Parry, PhD, Senior Consultant, Nexus Bonum, Australia
We are seeing growing interest in the use of ore sorting to achieve early-stage waste rejection and pre-concentration of lithium ores. In this presentation we discuss the rationale and potential benefits to be derived from introducing ore-sorter upgrade to lithium ores as well as the types of ore-sorting sensors finding application in this space, and sampling and test work programs required to assess viability-and finally-the current uptake in the Australian context.
Latest Developments in Direct Lithium Extraction (DLE)
Amir Razmjou, PhD, Associate Professor, Edith Cowan University
Transforming lithium recovery through advancements in Direct Lithium Extraction (DLE) technologies. Exploring cutting-edge methods, including membranes, adsorbents, and ion exchange systems in DLE technologies. Reducing material usage, simplifying processes, and enhancing selectivity by using DLE technologies. Supporting a low-carbon economy by minimising environmental impact with innovative DLE approaches.
17:05Happy Hour in the Exhibit Hall with Poster Viewing
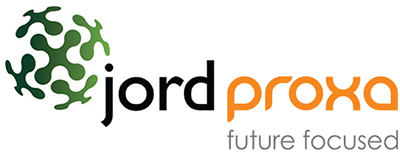
18:15Close of Day
Thursday, 22 May
07:00Presenter Briefing
07:30Registration Open
07:30Arrival Tea and Coffee in the Exhibit Hall with Poster Viewing
LITHIUM PROCESSING
Lewatit Ion Exchange Resins for Lithium Applications: Removal of New Emerging Contaminants Aluminium, Silica, and Boron
Dirk Steinhilber, PhD, Application Technology Manager, LANXESS Deutschland GmbH
The growing demand for battery-grade lithium requires efficient purification of lithium concentrates. Selective ion exchange resins are used to remove alkaline earth metals, boron, aluminium, and fluoride. Remarkably, we found that Lewatit chelating resin can be used in the H form for refining of LiHCO3 concentrates, without conversion with NaOH. Interestingly, when MonoPlus (630 µm - 650 µm) type resins are replaced by MDS (390 µm - 420 µm) resins, a significant increase in operating capacity was achieved. Thus, less regeneration steps are required, which allows savings on regeneration chemicals and longer resin lifetime Additionally, ultrapure lithium concentrates achieved.
Bulk Lithium Grade Measurement with Low Field Magnetic Resonance for Bulk Sorting and Monitoring
Peter Coghill, PhD, Group Leader & Principal Research Scientist, Magnetic Resonance Mineral Resources, CSIRO
In some cases, hard rock Lithium deposits are not amenable to rock-by-rock sorting or the required throughput is too high to efficiently sort the entire production stream. This talk discusses a bulk measurement technique that could be used for sorting these streams, while discussing the potential benefits and drawbacks of bulk sorting.
Novel Alkaline Leaching Processes for Various Lithium Minerals
Tian Zhang, Specialist, Hydrometallurgy, Metso
Reducing environmental impact while maintaining cost competitiveness is crucial for operators in the production of battery-grade lithium, both now and in the future. While spodumene is well-known as the primary source of lithium from hard rocks, the increasing demand for lithium has highlighted the importance of other lithium-bearing minerals. This paper presents the advancements in Metso’s alkaline leaching technologies for various lithium minerals, with a particular focus on petalite processing.
Continuous Ion Exchange in Lithium Processing: Direct Lithium Extraction and Refinery
Olga Yahorava, PhD, Principal Chemist, Clean TeQ Water
This presentation will cover direct lithium extraction, lithium refinery, absorbents and ion exchange materials. In additiona equipment options and benefits of continuous counter-current approach: moving bed will be discussed along with resin-in-solution, U-shaped column and examples of direct lithium extraction from different sources, and hardness removal from the lithium-rich stream.
10:35Sponsored Presentation (Opportunity Available)
11:05Morning Tea in the Exhibit Hall with Poster Viewing (Sponsorship Opportunity Available)
MINE WASTE STREAM AND TAILINGS REPROCESSING
Towards Critical Metal Recovery from Australia’s Mine Waste
Anita Parbhakar-Fox, PhD, Associate Professor, Sustainable Minerals Institute, The University of Queensland
This presentation will document finding from new geometallurgical research being undertaken by the University of Queensland across Australia to identify new critical metal mine waste (i.e., tailings, waste rock, slag, metallurgical residues) resources. Sites in Queensland, New South Wales, South Australia, Tasmania, and the Northern Territories have been sampled with new deposits of Co, REE, In and Sb in particular identified.
LITHIUM-BATTERY RECYCLING
Battery Recycling: A Key Solution to the Critical Mineral Supply Crisis
Mervyn Stevens, Vice President, Battery Minerals & Materials, Worley
Geopolitical tensions and growing demand from the energy transition are placing significant strain on the global supply of critical minerals. Battery recycling offers a sustainable solution to ease this pressure. However, widespread adoption is hindered by several challenges. This paper analyses the current obstacles facing the battery recycling sector and explores strategies to overcome them, unlocking its full potential for securing the mineral supply chain.
A Techno-Economic Study Examining Selected Options for Processing Black Mass
Michael Dry, PhD, Owner, Arithmetek, Canada
This presentation will cover a techno-economic evaluation of various technologies for the recycling of battery metals from black mass recovered from recycled lithium-ion batteries. The approach will entail process and cost modelling for each technology examined. he options will include published hydrometallurgical and pyrometallurgical routes, plus a novel route currently under development.
13:05Networking Luncheon (Sponsorship Opportunity Available)
LITHIUM-BATTERY RECYCLING
Recycling Spent Lithium Iron Phosphate (LFP) Batteries: Systematic Investigation of Pre-Treatment Schemes and Leaching Agent Efficiency
The increasing use of lithium iron phosphate (LFP) batteries, one of the fastest-growing types of lithium-ion batteries, is anticipated to significantly increase battery waste. This study investigates recycling spent LFP batteries through discharge, pre-treatment, and selective leaching. Discharged batteries underwent pyrolisis and shredding in three different schemes, followed by leaching with various leaching agent. Findings highlight the impact of pre-treatment and leaching agents on lithium recovery, contributing to an optimised recycling process.
The Future of Battery Recycling in South Korea: Government Policies, Industry Efforts, and Technological Breakthroughs
Mooki Bae, Scientific Researcher, Korea Institute of Geoscience & Mineral Resources KIGAM
South Korea’s battery recycling industry is rapidly advancing with a focus on efficient resource recovery, eco-friendly technology, and robust end-of-life battery management systems. Supported by government policies, the industry aims to optimise metal recovery, build a circular economy, and comply with environmental standards. As global demand rises, South Korea is positioned to lead the battery recycling market, setting a sustainable model for resource management and environmental responsibility.
Classification of Intermediate Recycled Li-ion Battery Materials
Jamie Weaver, PhD, Research Chemist, Material Measurement Lab, NIST
Intermediate recycled lithium-ion battery material, called black mass, is produced from manufacturing scraps and used cells. The diversity of source materials, which include different chemistries such as LFP, NMC, and LCO, leads to variations in product quality. Establishing a harmonised classification system based on material composition could enhance market dynamics and trade while supporting a circular economy for battery materials. This presentation will discuss current research and future efforts in this area.
15:35Afternoon Tea in the Exhibit Hall with Poster Viewing (Sponsorship Opportunity Available)
Advanced Lithium Processing Methods-Opportunities & Illusions
Adrian Griffin, Principal, Future Technology Trust
This panel discussion will explore the latest innovations in lithium extraction and refinement technologies. Experts will examine the potential of cutting-edge methods to meet the growing demand for lithium in electric vehicles and energy storage. The conversation will also address the challenges, economic viability, and environmental impacts, distinguishing between genuine opportunities and overhyped claims within the rapidly evolving lithium industry.
17:05Close of Conference
* 活動內容有可能不事先告知作更動及調整。